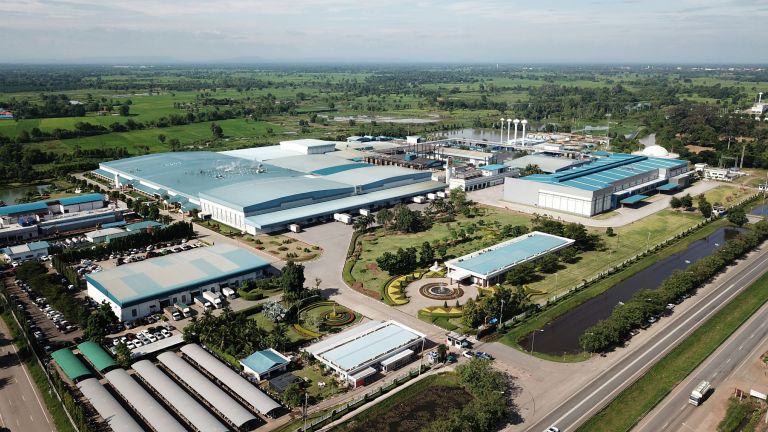

Charoen Pokphand Foods Public Company Limited (CP Foods) is going through a digital makeover to raise the standard of chicken production processes throughout the value chain, making the products more traceable, safer and environmental friendlier.
Panuwat Niamprem, senior vice president of CP Foods, said the company has adopted multiple digital innovations that connect all of the supply chain together and build up a smarter, more efficient and more sustainable ecosystem. He further explained that Artificial Intelligence (AI) and Internet of Things (IoT) has linked all the operations together from feed production to its chicken farms, offices and processing plant all over Thailand.
Moreover, automation has been adopted in many of its factories. Currently, the broiler complexes in Nakhon Ratchasima, Saraburi, and Minburi are pilot models for CP Foods’ “Smart Farm and Smart Factory” projects. The integration of AI and IoT in these pilot operations has helped CP Foods to collect, traceback and getting for insightful data and, as a result, leading to better decisions and production planning.
"Digital transformation is helping us to gain more productivity and better strategy. It also improve food safety as ingredients and processes can be traceable throughout the production chain. Moreover, technology such as automation enables us to maintain minimal human contact, reduces wastage, reduces unnecessary costs and risks in production and transportation, " said Mr. Panuwat.
These technologies also give farmed chickens a better life. CP Foods’ broiler business has adopted the Smart Farm system to increase production efficiency and promote animal welfare in broiler farms in addition to treating animals with care. The farms installed devices to monitor the well-being of animals such as an anemometer, temperature meter, ammonia meter, Carbon Dioxide Meter and Automatic feeding equipment that can control all devices through a computer system and CCTV, which can bring the data pool to analyze and keep inform of Big Data.
“The implementation of AI and IoT enable us to get high-precision data collection for analysis and planning. The data pool are collected in our tailor-made application. This enables us to monitor and evaluate the value chain in Real Time and in all locations via mobile phone. We can make faster decisions and solve problems on the spot quickly and, more importantly, it helps in term of traceability,” he said.
In processing phase, CP Foods applies various auto machines such as Auto Cutting Machine, BL Deboner, BB Deboner, Block Steak and Water Jet cutting machine to improve cutting efficiency. The raw products then will be cooked by machines, packed, and managed by robots to minimize risk of contamination from human.
Panuwat added that CP Foods has been certified for the “PS 7818: 2018; CPF Food Safety, Quality and Sustainability Management System” standard, dubbed as “CPF Food Standard, by BSI Group (Thailand) Co., Ltd, for its products made in the Company’s Chicken business in Korat Model, Nakhon Ratchasima province. The pilot project or “Korat Model”, is aimed at assuring global consumers of a single standard on product quality, safety and sustainability.
Aside Iot and AI, CP Foods chicken businesses has transition toward a greener grid with a goal to phase out coal-fired power, replacing with alternative energy sources such as biogas, bi0mass and solar power.